Dunkin’ Donuts, a beloved American institution, is more than just a coffee shop. It’s a place where friends meet, families grab a quick breakfast, and the aroma of freshly brewed coffee and sweet treats fills the air. With thousands of locations across the globe, Dunkin’ has become a symbol of American coffee culture, offering a wide variety of beverages and, of course, its iconic donuts.
However, recent headlines have been dominated by a concerning issue: the Dunkin’ Doughnut Shortage. Customers have been met with empty shelves and disappointed faces as their favorite glazed, chocolate, or jelly donuts have mysteriously vanished. This Dunkin’ Doughnut Shortage has not only impacted the company’s bottom line but has also sparked curiosity and concern among its loyal customer base. Â
Understanding the reasons behind this dunkin’ doughnut shortage is crucial. It allows us to appreciate the complex supply chains that bring our favorite treats to our doorsteps and to gain a deeper understanding of the challenges faced by businesses in today’s interconnected world. So, let’s dive into the top 10 reasons behind the Dunkin’ Doughnut Shortage and uncover the factors contributing to this sweet crisis.
Also Read : 10 Best Online Data Science Degree for Your Career
1. Supply Chain Disruptions : Dunkin’ Doughnut Shortage
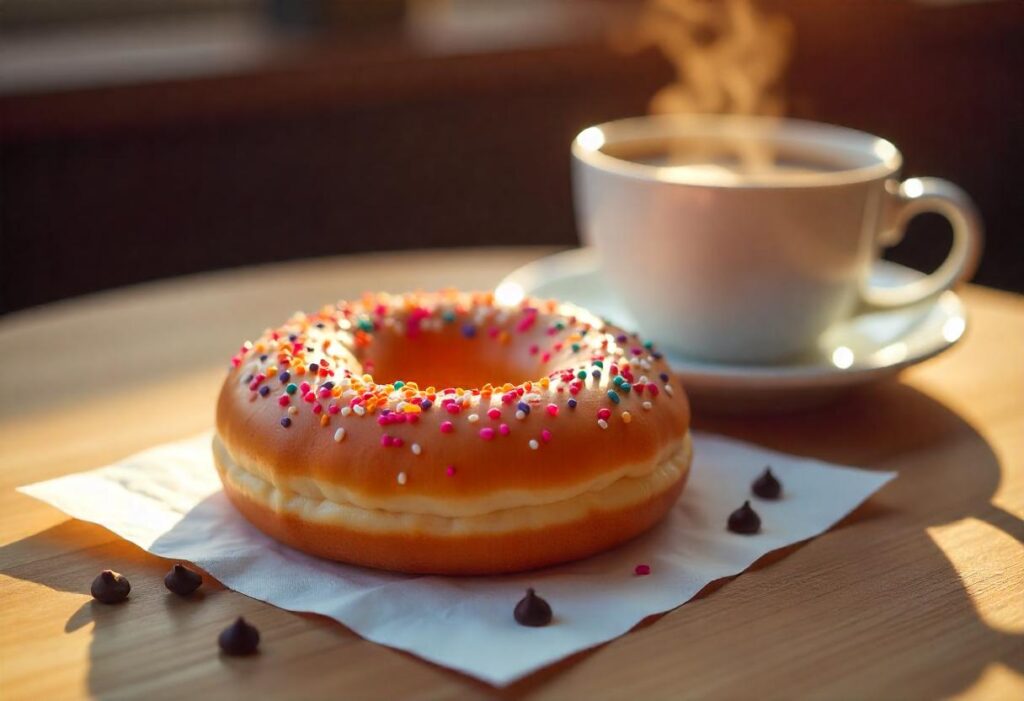
In today’s interconnected world, our daily lives are deeply intertwined with global supply chains. These intricate networks transport raw materials, ingredients, and finished goods across continents, ensuring that products reach our shelves. However, these supply chains are incredibly fragile and susceptible to disruptions.
The food industry, in particular, relies heavily on a robust and efficient supply chain. From the farm to the factory and ultimately to our plates, a multitude of factors can disrupt this delicate balance. These disruptions can include:
- Natural Disasters: Events like hurricanes, floods, and droughts can devastate crops, damage transportation infrastructure, and cripple food production.
- Pandemics: Global health crises, such as the recent COVID-19 pandemic, can lead to labor shortages, factory closures, and transportation bottlenecks, severely impacting the movement of goods.
- Geopolitical Unrest: Wars, conflicts, and political instability can disrupt trade routes, increase transportation costs, and hinder the flow of goods across borders.
- Increased Demand: Unexpected surges in demand, such as during holidays or special events, can overwhelm supply chains, leading to shortages and delays.
Specific Effects on the Dunkin’ Doughnut Shortage
The Dunkin’ Doughnut Shortage is likely a result of various supply chain disruptions. For example:
- Ingredient Shortages: Key ingredients used in donut production, such as flour, sugar, and oils, may have experienced shortages due to factors like adverse weather conditions impacting crops or disruptions in the transportation of these commodities.
- Labor Shortages: The pandemic significantly impacted the labor market, leading to staffing shortages at various levels of the supply chain, from farmers and truck drivers to factory workers and delivery personnel.
- Transportation Bottlenecks: Global shipping delays and increased transportation costs, exacerbated by the pandemic and other factors, may have hindered the timely delivery of ingredients and finished products to Dunkin’ Donuts locations.
These disruptions on the Dunkin’ Doughnut Shortage can create a domino effect, impacting production schedules, delaying deliveries, and ultimately leading to empty shelves and frustrated customers.
Also Read : The Robin Hood Tax: Solution for Wealth Disparity in 2025
2. Ingredient Shortages : Dunkin’ Doughnut Shortage
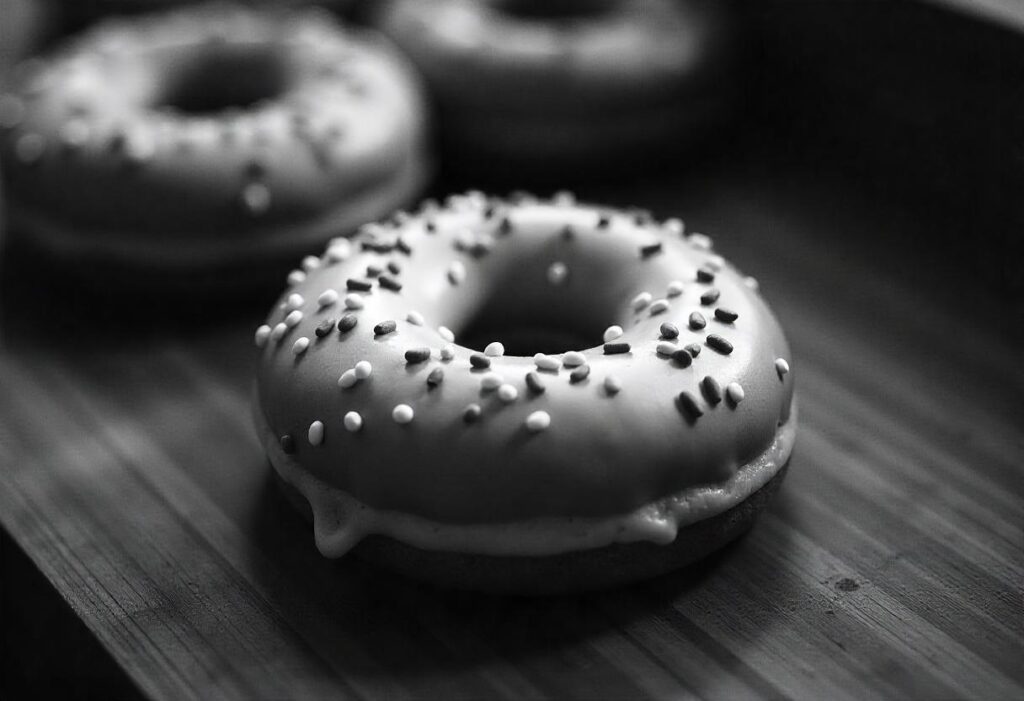
Cause of Dunkin’ Doughnut Shortage, Dunkin’ Donuts, like any food manufacturer, relies on a diverse array of ingredients to create its beloved menu items. Some of the key ingredients crucial for donut production include:
- Flour: A fundamental component of dough, flour is a staple ingredient in large quantities.
- Sugar: Used for both sweetening the dough and creating glazes and icings.
- Eggs: Essential for binding the dough and contributing to its texture.
- Milk: Used in various stages of the production process, from dough preparation to coffee beverages.
- Yeast: A crucial ingredient for dough rising.
- Vegetable Oils: Used for frying the donuts.
- Cocoa Powder: For chocolate-flavored donuts.
- Fruits and Nuts: For fillings and toppings, such as jelly, sprinkles, and nuts.
Challenges in Procuring Ingredients Amid Global Crises
Procuring these ingredients can be challenging, especially in the face of global crises:
- Supply Chain Disruptions: As discussed earlier, disruptions in global supply chains can significantly impact the availability and cost of ingredients. Delays in transportation, port congestion, and border closures can hinder the timely delivery of raw materials to processing plants.
- Weather Impacts on Agriculture: Adverse weather conditions, such as droughts, floods, and extreme temperatures, can severely impact crop yields, leading to shortages and price fluctuations of essential ingredients like flour, sugar, and fruits.
- Geopolitical Unrest: Conflicts, trade wars, and political instability can disrupt agricultural production and trade routes, impacting the availability and cost of ingredients.
- Increased Demand: Growing global demand for food, coupled with changing dietary preferences, can put a strain on agricultural production and increase competition for essential ingredients.
These challenges can force companies like Dunkin’ Donuts to navigate fluctuating ingredient prices, seek alternative suppliers, and potentially adjust their recipes to accommodate ingredient shortages.
Also Read : 10 Proven Ways to Make Money with Canva in 2025
3. Labor Shortages in the Food Industry : Dunkin’ Doughnut Shortage
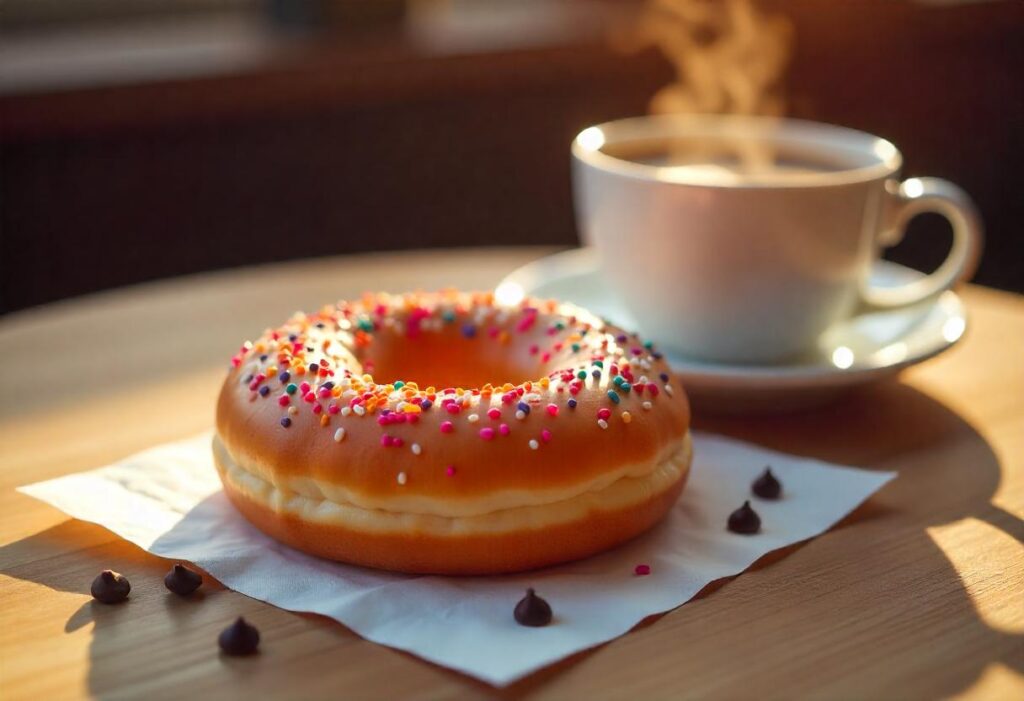
The food industry, from farm to table, relies heavily on a robust workforce. However, recent years have witnessed a significant shortage of workers across various sectors within the industry. This labor shortage has had a cascading effect, impacting production, distribution, and ultimately, the availability of products like Dunkin’ Donuts.
Impact of Workforce Shortages on Production
Labor shortages can significantly disrupt the production process in several ways:
- Reduced Production Capacity: With fewer workers available, factories and processing plants may be unable to operate at full capacity, leading to decreased production output.
- Delayed Production Cycles: Insufficient staffing can lead to slower production lines, longer processing times, and delays in getting products to market.
- Increased Costs: Businesses may be forced to increase wages to attract and retain workers, leading to higher production costs and potentially impacting product prices.
- Reduced Quality Control: Labor shortages can also impact quality control measures, as there may be fewer workers available to inspect products and ensure they meet safety and quality standards.
How This Contributed to the Dunkin’ Doughnut Shortage
Labor shortages within the food industry likely played a role in the Dunkin’ Doughnut Shortage. For example:
- Shortages at Production Facilities: A lack of workers at donut production facilities could have slowed down production lines, leading to delays in meeting demand.
- Transportation and Logistics Challenges: Driver shortages within the trucking industry could have disrupted the timely delivery of ingredients and finished products to Dunkin’ Donuts locations.
- Staffing Issues at Retail Locations: Understaffed Dunkin’ Donuts stores may have struggled to keep up with customer demand, leading to longer wait times and potentially impacting the overall customer experience.
Addressing labor shortages within the food industry is crucial for ensuring a stable and reliable supply chain. This may involve initiatives such as:
- Improving working conditions and wages: Attracting and retaining workers by offering competitive wages, benefits, and safe working environments.
- Investing in employee training and development: Providing opportunities for career advancement and skill development to enhance employee satisfaction and retention.
- Promoting the food industry as a viable career path: Raising awareness of the diverse career opportunities available within the food industry.
By addressing these challenges, the food industry can ensure a more stable and resilient workforce, ultimately benefiting businesses like Dunkin’ Donuts and ensuring a consistent supply of their beloved products.
Also Read : 12 Key Factors Affecting Aviation Fuel Prices You Should Know
4. Increased Consumer Demand : Dunkin’ Doughnut Shortage
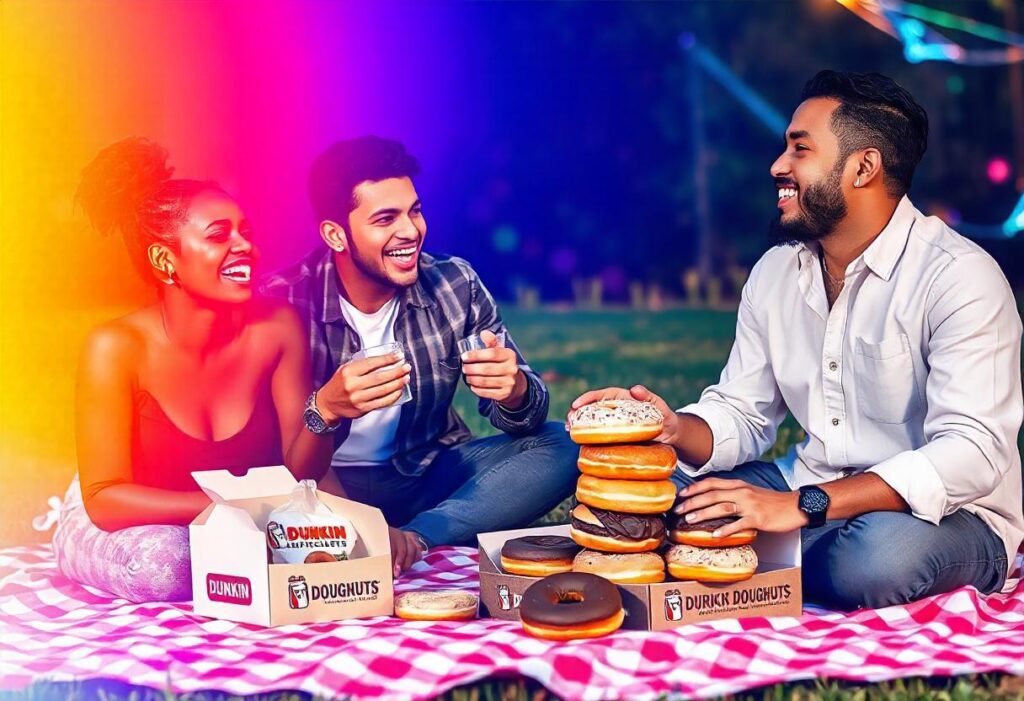
The COVID-19 pandemic brought about significant changes in consumer behavior, including a surge in demand for Dunkin’ Donuts. This increased demand, while seemingly positive, also contributed to the shortage.
Rising Popularity of Dunkin’ Donuts During the Pandemic
Several factors contributed to the increased popularity of Dunkin’ Donuts during the pandemic:
- Shift to Remote Work: With many people working from home, the daily routine of grabbing coffee and a donut on the way to work was disrupted. Dunkin’ Donuts, with its convenient drive-thru locations, became an attractive option for a quick and satisfying breakfast or mid-morning pick-me-up.
- Increased Comfort Food Consumption: During times of stress and uncertainty, many people turn to comfort foods for solace. Dunkin’ Donuts, with its sweet and satisfying treats, likely experienced an increase in demand as people sought familiar and comforting indulgences.
- Focus on Essential Businesses: As non-essential businesses were forced to close, Dunkin’ Donuts, as a provider of essential food and beverages, remained open, further solidifying its position as a go-to destination for many consumers.
Why Sudden Demand Led to Shortages
While increased demand is generally positive for a business, a sudden and unexpected surge in demand can strain even the most efficient supply chains. In the case of Dunkin’ Donuts:
- Production Bottlenecks: Increased demand may have overwhelmed production facilities, leading to longer production times and delays in meeting order volumes.
- Inventory Challenges: The sudden surge in demand may have caught Dunkin’ Donuts off guard, leading to depleted inventory levels and difficulties in keeping up with customer orders.
- Distribution Challenges: Increased demand may have strained distribution networks, leading to delays in delivering products to stores and potentially impacting the availability of certain items.
While increased demand is a testament to the popularity of Dunkin’ Donuts, it also highlights the importance of agile supply chains that can adapt to fluctuating demand and ensure a consistent supply of products.
5. Transportation and Logistics Issues : Dunkin’ Doughnut Shortage
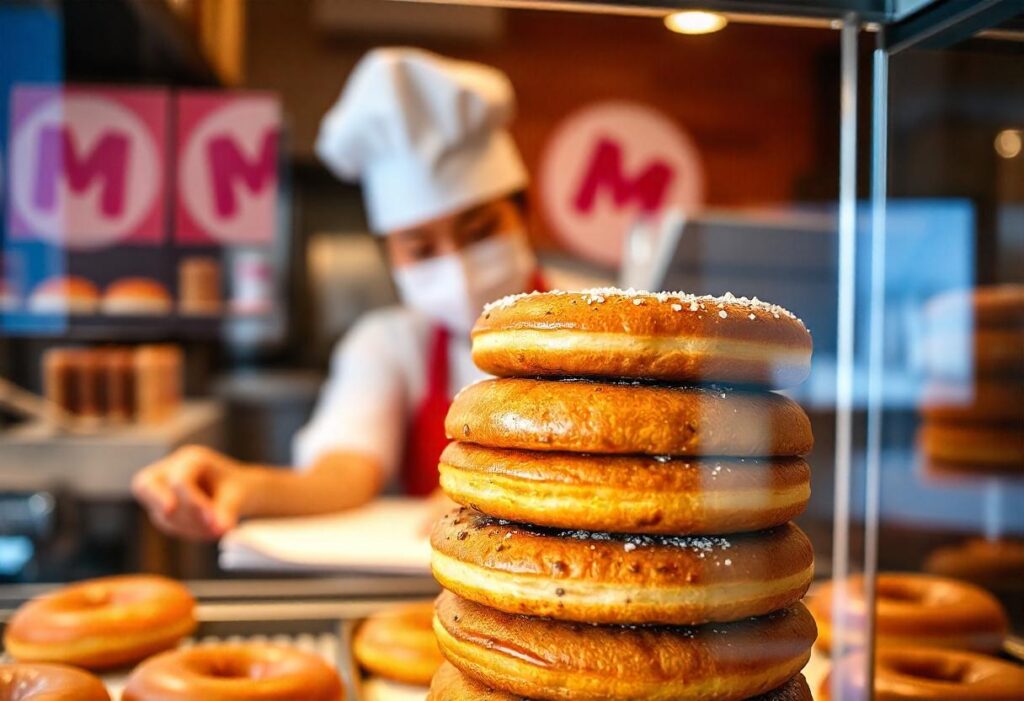
Transportation and logistics play a critical role in ensuring that products like Dunkin’ Donuts reach stores efficiently. However, recent years have seen significant disruptions in global shipping and transportation networks, impacting businesses across various sectors.
Global Shipping Delays and Rising Costs
Several factors have contributed to these disruptions:
- Container Shortages: The COVID-19 pandemic led to a surge in demand for goods, particularly consumer goods, while simultaneously disrupting production and transportation networks. This mismatch between supply and demand created a shortage of shipping containers, leading to longer wait times and increased costs.
- Port Congestion: Major ports around the world experienced severe congestion, with ships waiting for days or even weeks to unload. This backlog further exacerbated delays and increased transportation costs.
- Fuel Price Volatility: Fluctuating fuel prices, driven by geopolitical events and economic uncertainty, have significantly increased transportation costs for businesses.
- Driver Shortages: The trucking industry has faced a significant shortage of drivers, impacting the timely delivery of goods across the country.
The Role of Transportation Hiccups in the Dunkin’ Doughnut Shortage
Transportation and logistics issues have likely played a role in the Dunkin’ Doughnut Shortage:
- Delayed Ingredient Deliveries: Delays in shipping and transportation can hinder the timely delivery of key ingredients to Dunkin’ Donuts’ production facilities, impacting production schedules.
- Increased Costs: Rising transportation costs can impact the overall cost of production, potentially squeezing profit margins and making it more challenging for Dunkin’ Donuts to maintain competitive pricing.
- Distribution Challenges: Delays in transportation can disrupt the distribution of finished products to Dunkin’ Donuts stores, leading to stockouts and empty shelves.
Addressing these transportation and logistics challenges is crucial for ensuring a stable and efficient supply chain for businesses like Dunkin’ Donuts. This may involve initiatives such as:
- Investing in infrastructure: Improving port capacity and expanding transportation networks to alleviate congestion and reduce delays.
- Promoting alternative modes of transportation: Exploring options like rail and inland waterways to reduce reliance on ocean shipping.
- Addressing labor shortages: Implementing measures to attract and retain truck drivers, such as improving working conditions and wages.
By addressing these challenges, businesses can navigate the complexities of global supply chains and ensure a consistent supply of products to meet consumer demand.
6. Unforeseen Weather Conditions : Dunkin’ Doughnut Shortage
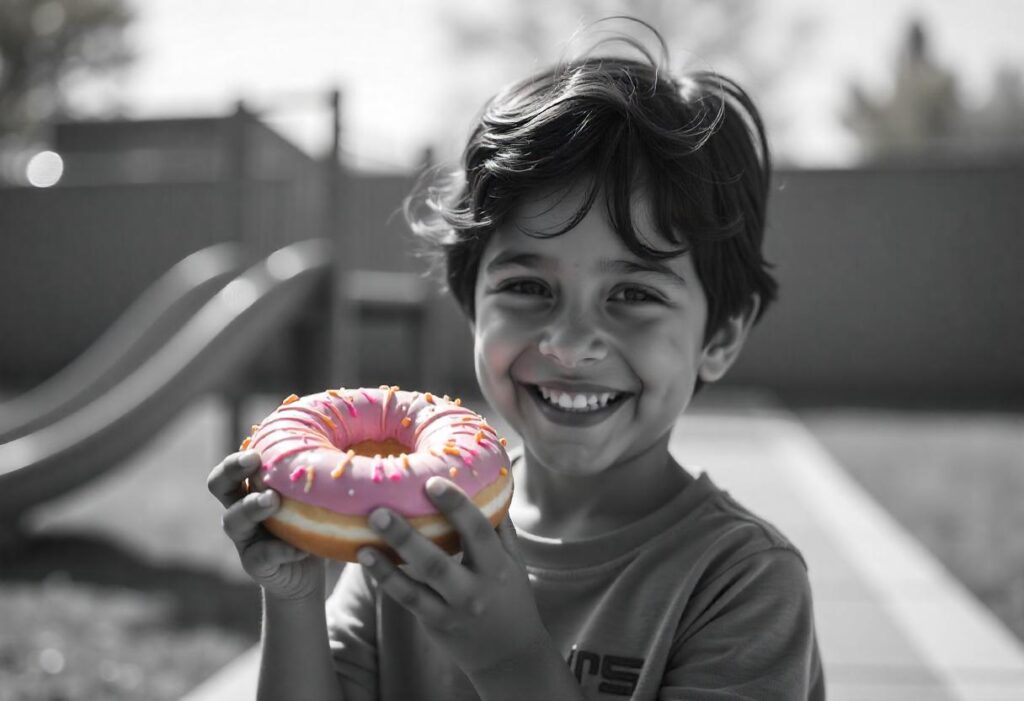
Unforeseen weather conditions can wreak havoc on agricultural production and transportation networks, significantly impacting the availability of key ingredients for Dunkin’ Donuts.
Natural Disasters and Their Effects on Dunkin’ Doughnut Shortage Ingredients
Natural disasters such as:
- Droughts: Can lead to crop failures, impacting the production of essential ingredients like wheat (for flour) and sugar.
- Floods: Can devastate crops, damage transportation infrastructure, and contaminate water supplies used in food production.
- Hurricanes and Storms: Can disrupt transportation networks, damage crops, and disrupt power grids, halting production at processing plants.
How This Played a Role in the Dunkin’ Doughnut Shortage
Adverse weather conditions can directly impact the availability of ingredients for Dunkin’ Donuts:
- Reduced Crop Yields: Droughts and floods can significantly reduce crop yields, leading to shortages and price increases for essential ingredients like wheat, sugar, and fruits.
- Transportation Disruptions: Severe weather events can damage roads, bridges, and other transportation infrastructure, hindering the movement of ingredients and finished products.
- Production Delays: Power outages caused by storms can disrupt production at processing plants, leading to delays and potential production losses.
By monitoring weather patterns and implementing contingency plans, businesses like Dunkin’ Donuts can mitigate the impact of unforeseen weather events on their supply chains.
7. Pandemic-Driven Changes in Consumer Habits : Dunkin’ Doughnut Shortage
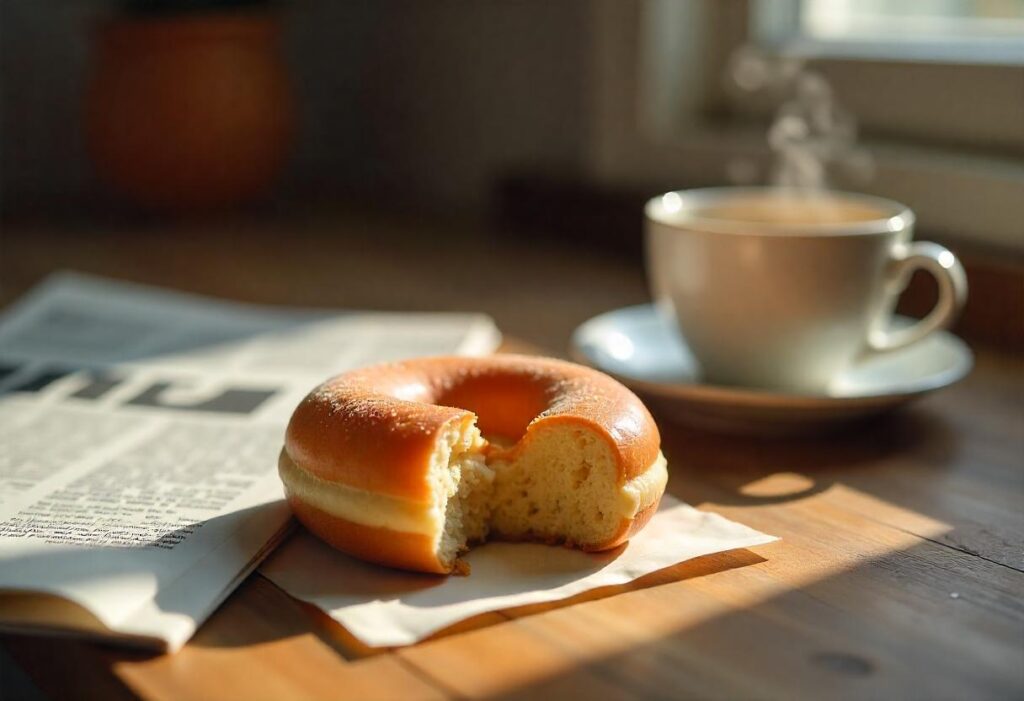
The pandemic really changed how people lived and shopped. 1 One big change was the rise of online ordering. 2 Suddenly, everyone was ordering groceries, clothes, and even coffee online! This shift in how people got their food and drinks had a big impact on businesses like Dunkin’.
Growth of Online Orders and Its Impact on Supply
With more people ordering their Dunkin’ fix online and through apps, the demand for delivery and to-go orders skyrocketed. This meant that Dunkin’ had to:
- Increase production to meet the higher demand: More orders meant more donuts, coffee, and other items needed to be made.
- Adjust their supply chain: They needed to make sure they had enough ingredients and supplies to keep up with the increased demand for delivery and to-go orders.
- Ensure timely delivery: Getting orders to customers quickly and accurately became even more important.
How Dunkin’ Struggled to Keep Up
While the increase in online orders was good for business, it also presented some challenges for Dunkin’.
- Increased pressure on supply chains: The sudden surge in demand could have strained their supply chains, leading to potential shortages of ingredients or delays in getting products to stores.
- Adjusting to new delivery models: Meeting the demands of online orders and delivery services required adjustments to their operations, which can take time and resources.
Despite these challenges, Dunkin’ has been working hard to adapt to these changes in consumer behavior and continue to provide their customers with their favorite treats.
8. Rising Costs of Production : Dunkin’ Doughnut Shortage
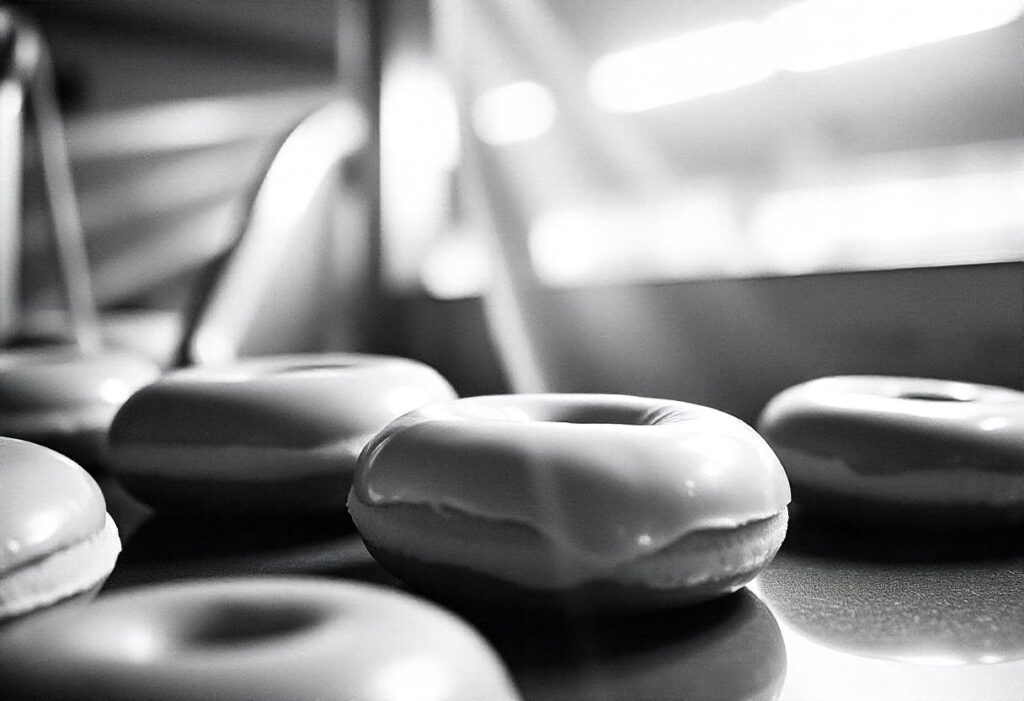
You know how sometimes your favorite toys or snacks cost a little more at the store? Well, that’s because making things can get more expensive too! This is called inflation, and it’s been happening lately.
Dunkin’ Doughnut Shortage has been affected by this too. Here’s how:
- Ingredient Costs: As we discussed earlier, things like flour, sugar, and even the milk for your coffee can cost more to produce. This means Dunkin’ Donuts has to pay more for the ingredients to make your favorite treats.
- Labor Costs: When workers need to be paid more to make a living, it costs businesses like Dunkin’ Donuts more to make and serve your donuts.
- Energy Costs: Making donuts uses energy, like electricity and gas. When energy costs go up, it makes it more expensive for Dunkin’ Donuts to keep the lights on and the ovens running.
These increased costs can put a squeeze on Dunkin’ Donuts’ profits. Sometimes, businesses might need to raise prices to cover these extra expenses.
9. Bakery-Specific Challenges : Dunkin’ Doughnut Shortage
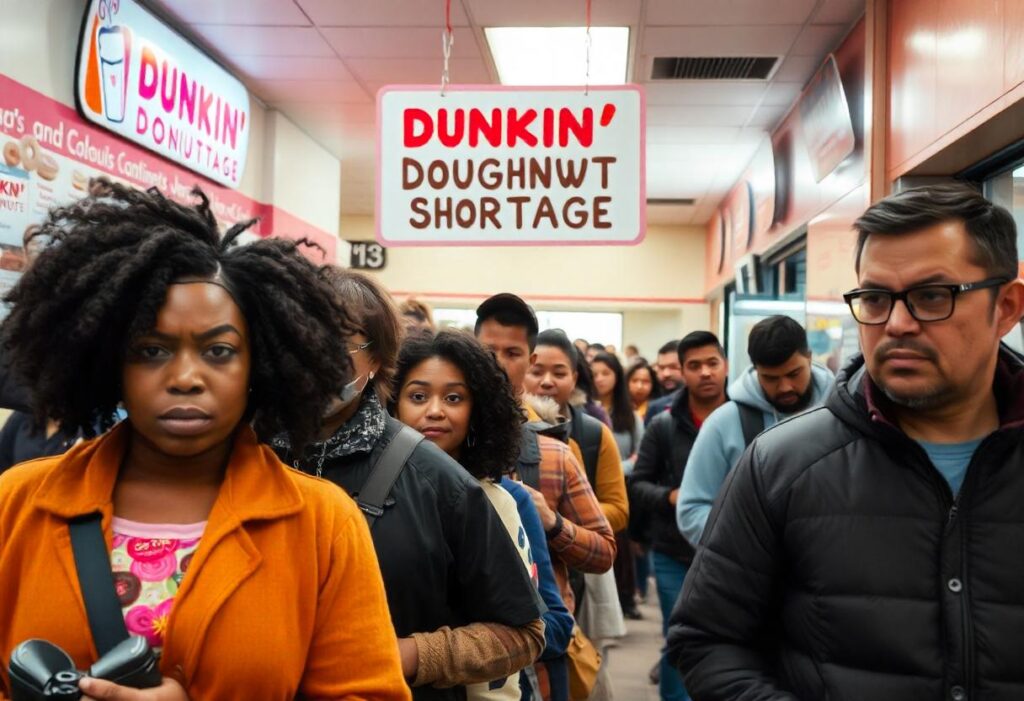
Dunkin’ Donuts, with its thousands of locations worldwide, faces unique challenges in maintaining consistent quality and supply across its vast network.
Challenges Faced by Local Dunkin’ Bakeries
- Maintaining Consistent Quality: Ensuring that every glazed donut, every chocolate frosted, tastes exactly the same in every location is a huge challenge. Factors like local ingredient variations, differences in baking equipment, and even varying levels of staff training can all impact the final product.
- Managing Inventory: Predicting demand for different donut varieties across numerous locations can be tricky. Overstocking can lead to waste, while understocking can disappoint customers and result in lost sales.
- Staffing and Training: Ensuring that every bakery has the right number of skilled bakers and baristas is crucial for efficient operations and consistent product quality.
Struggles in Maintaining Consistency Across Locations
- Regional Differences: Customer preferences can vary significantly from region to region. What’s a popular donut in one city might not be as popular in another.
- Supply Chain Variations: Local supply chains can differ in terms of reliability and the availability of fresh ingredients.
- Competition: Dunkin’ Donuts faces competition from local bakeries and other coffee chains, each with its own unique offerings and customer base.
Despite these challenges, Dunkin’ Donuts continues to work hard to maintain consistent quality and customer satisfaction across its global network.
10. Lack of Forward Planning : Dunkin’ Doughnut Shortage
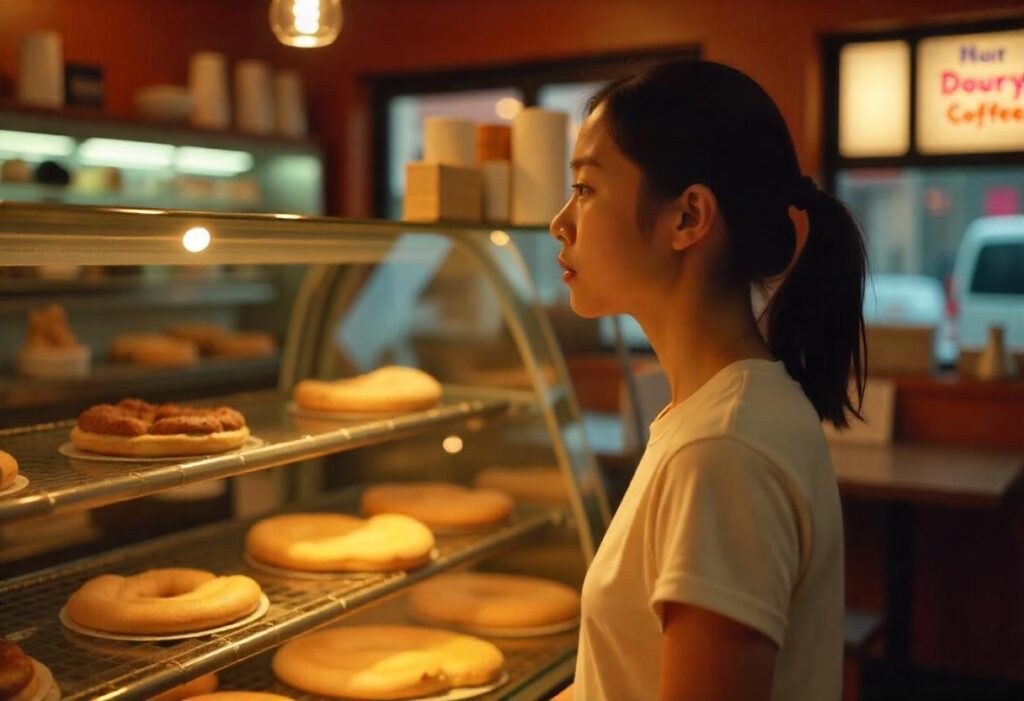
Sometimes, even the best companies can run into trouble if they don’t plan ahead. This can be true for Dunkin’ Donuts too.
How Insufficient Planning Led to the Dunkin’ Doughnut Shortage
- Not anticipating demand surges: If Dunkin’ didn’t accurately predict the increase in demand for their products, especially during the pandemic, they might not have had enough ingredients or staff to keep up.
- Not having backup plans: If something unexpected happened, like a severe weather event or a sudden shortage of a key ingredient, having a backup plan could have helped minimize the impact on donut production.
- Not investing in supply chain resilience: Building a more flexible and resilient supply chain can help businesses weather unexpected challenges, such as those caused by global events or natural disasters.
Lessons for the Future to avoid Dunkin’ Doughnut Shortage
Dunkin’ Donuts, like any business, can learn from these challenges. By:
- Improving forecasting: Better predicting future demand can help them ensure they have the resources to meet customer needs.
- Diversifying their supply chain: Relying on multiple suppliers for key ingredients can help minimize the impact of disruptions.
- Investing in technology: Using technology to track inventory, monitor supply chains, and improve communication can help them respond more quickly to challenges.
By learning from these experiences, Dunkin’ Donuts can improve its operations, better serve its customers, and ensure that everyone can enjoy their favorite donuts.
Impact of the Dunkin’ Doughnut Shortage on Customers and the Brand
The Dunkin’ Doughnut Shortage had a significant impact on both customers and the brand itself, extending beyond initial frustrations and social media outrage.
Customer Reactions and Social Media Outrage on the Dunkin’ Doughnut Shortage:
- Frustration and Disappointment: Customers expressed widespread frustration and disappointment at the inability to enjoy their favorite Dunkin’ treats. Many felt let down by the brand they had come to rely on for their daily coffee and donut fix.
- Social Media Explosion: The shortage quickly became a social media phenomenon. Hashtags like #DunkinShortage and #DoughnutGate trended, with customers sharing humorous memes, creative coping mechanisms (like attempting to bake their own donuts), and venting their frustrations.
- Erosion of Customer Loyalty: For some customers, the shortage may have eroded their loyalty to the brand. They might have switched to competitors like Krispy Kreme or local bakeries, seeking alternatives that could consistently provide them with their desired treats.
Effects on Brand Reputation:
- Negative Publicity: The widespread media coverage of the shortage, coupled with the negative social media buzz, undoubtedly impacted Dunkin’ Donuts’ brand image. The company faced criticism for its inability to maintain a consistent supply of its signature product.
- Damage to Brand Trust: The shortage could have shaken customer trust in Dunkin’ Donuts’ ability to consistently deliver on its promises. Customers might have questioned the brand’s reliability and its ability to manage its supply chain effectively.
- Potential for Long-Term Impact: The negative publicity and damage to brand trust could have long-term consequences for Dunkin’ Donuts. Rebuilding customer trust and loyalty requires consistent effort and a strong focus on customer satisfaction.
To mitigate the negative impact on its brand, Dunkin’ Donuts likely focused on:
- Open and Transparent Communication: Keeping customers informed about the situation and the steps being taken to address the shortage through official statements, social media updates, and in-store signage.
- Customer Service Initiatives: Implementing measures to compensate customers for the inconvenience caused by the shortage, such as offering discounts, coupons, or freebies.
- Reinforcing Brand Values: Emphasizing the quality and freshness of their products, as well as their commitment to customer satisfaction, through marketing campaigns and in-store experiences.
- Focus on Product Innovation: Introducing new and exciting donut flavors and menu items to re-engage customers and generate positive buzz.
By proactively addressing these challenges and focusing on rebuilding customer trust, Dunkin’ Donuts can strive to regain its position as a beloved and reliable brand in the coffee and donut market.
What Dunkin’ Is Doing to Address the Shortage
Dunkin’ Donuts, like any major food service company, likely implemented a multi-pronged approach to address the shortage and prevent future occurrences:
- Supply Chain Optimization:
- Diversification of Suppliers: Exploring alternative suppliers for key ingredients to reduce reliance on a single source and mitigate the impact of potential disruptions.
- Strengthening Logistics: Improving transportation and logistics networks to ensure timely delivery of ingredients and finished products. This may involve optimizing routes, investing in technology for better tracking, and exploring alternative transportation methods.
- Inventory Management: Implementing more robust inventory management systems to accurately forecast demand, optimize stock levels, and minimize waste.
- Production Enhancements:
- Increased Production Capacity: Evaluating and potentially expanding production capacity to meet increased demand, especially during peak periods.
- Improved Production Processes: Streamlining production processes to increase efficiency and reduce bottlenecks.
- Enhanced Quality Control: Implementing stricter quality control measures to ensure consistent product quality and minimize waste.
- Technology Integration:
- Data Analytics: Leveraging data analytics to gain deeper insights into customer demand, identify potential disruptions, and optimize operations.
- Digital Platforms: Investing in digital platforms and mobile apps to enhance the customer experience, improve order accuracy, and facilitate smoother delivery operations.
- Communication and Transparency:
- Open Communication with Customers: Keeping customers informed about the situation and the steps being taken to address the shortage through official statements, social media updates, and in-store signage.
- Building Customer Relationships: Implementing loyalty programs and other initiatives to rebuild customer trust and loyalty.
Future Plans to Prevent Similar Issues:
- Scenario Planning and Risk Mitigation: Developing robust contingency plans to address potential disruptions, such as natural disasters, pandemics, and geopolitical events.
- Continuous Improvement: Regularly reviewing and improving supply chain processes, production methods, and operational strategies to ensure long-term sustainability and resilience.
- Investing in Innovation: Exploring innovative technologies and approaches to improve efficiency, reduce waste, and enhance the overall customer experience.
By implementing these strategies, after the dunkin’ doughnut shortage, Dunkin’ Donuts can strive to build a more resilient and sustainable supply chain, ensuring a consistent supply of its beloved products and maintaining its position as a leading brand in the coffee and donut market.
How Customers Can Cope with the Dunkin’ Doughnut Shortage
While the Dunkin’ Doughnut Shortage was undoubtedly frustrating for many, customers can find ways to cope and even support local businesses during such times.
After the Dunkin’ Doughnut Shortage, Tips for Finding Alternatives:
- Explore Local Bakeries: Discover the hidden gems in your community! Many local bakeries offer delicious and unique donut varieties.
- Embrace Other Treats: Indulge in other Dunkin’ menu items like muffins, bagels, or breakfast sandwiches.
- Try Baking at Home: Get creative in the kitchen and try your hand at baking your own donuts. There are plenty of easy recipes available online.
- Embrace the Coffee: Enjoy your favorite Dunkin’ coffee and explore other beverage options like iced teas or refreshers.
Supporting Local Stores During Shortages:
- Patronize Local Bakeries: Show your support for local businesses by patronizing them during shortages.
- Spread the Word: Recommend your favorite local bakeries to friends and family.
- Leave Positive Reviews: Share your positive experiences at local bakeries through online reviews and social media.
While the Dunkin’ Doughnut Shortage was a temporary setback, it presented an opportunity for customers to discover new favorites and support their local communities.
The Dunkin’ Doughnut Shortage : A Case Study in the Challenges Facing the Modern Food Industry
The Dunkin’ Doughnut Shortage served as a stark reminder of the complex and interconnected nature of the modern food system. From global supply chain disruptions and ingredient shortages to labor challenges and rising production costs, numerous factors contributed to this temporary setback.
Recap of the Top 10 Reasons Behind the Dunkin’ Doughnut Shortage:
- Supply Chain Disruptions: Global supply chain disruptions, including those caused by natural disasters, pandemics, and geopolitical unrest, significantly impacted the availability of ingredients and the timely delivery of products.
- Ingredient Shortages: Shortages of key ingredients such as flour, sugar, and oils, driven by factors like adverse weather conditions and increased global demand, impacted donut production.
- Labor Shortages: Labor shortages across the food industry, from farms to factories and transportation, impacted production capacity and delivery timelines.
- Increased Consumer Demand: The surge in demand for Dunkin’ Donuts during the pandemic, driven by factors like remote work and increased comfort food consumption, strained supply chains and production capacity.
- Transportation and Logistics Issues: Global shipping delays, port congestion, and rising transportation costs due to fuel price volatility and driver shortages impacted the timely delivery of ingredients and finished products.
- Unforeseen Weather Conditions: Adverse weather events like droughts, floods, and storms impacted crop yields, damaged transportation infrastructure, and disrupted production.
- Rising Production Costs: Inflation, driven by rising ingredient costs, labor costs, and energy costs, increased production expenses and potentially impacted product pricing.
- Pandemic-Driven Changes in Consumer Habits: The shift towards online ordering and increased demand for delivery services presented new challenges for Dunkin’ Donuts’ operations.
- Bakery-Specific Challenges: Maintaining consistent quality across numerous locations, managing inventory, and addressing regional variations in demand and supply chains posed unique challenges for Dunkin’ Donuts.
- Lack of Forward Planning: Insufficient planning and a lack of robust contingency plans to address unexpected challenges contributed to the shortage.
The Importance of Resilience in the Food Industry:
The Dunkin’ Doughnut Shortage underscored the importance of building a resilient and adaptable food system. This includes:
- Investing in sustainable agriculture: Promoting sustainable farming practices to ensure a stable and reliable supply of food.
- Strengthening supply chains: Diversifying suppliers, improving logistics infrastructure, and investing in technology to enhance supply chain visibility and resilience.
- Addressing labor challenges: Investing in workforce development, improving working conditions, and promoting the food industry as a viable career path.
- Embracing innovation: Exploring and adopting new technologies and approaches to improve efficiency, reduce waste, and enhance the overall sustainability of the food system.
By learning from these challenges and implementing proactive measures, the food industry can better navigate future disruptions and ensure a consistent supply of safe and affordable food for all.
The Dunkin’ Doughnut Shortage served as a stark reminder of the complex and interconnected nature of the modern food system. From global supply chain disruptions to unforeseen weather events, numerous factors can impact the availability of even the most beloved treats. By understanding these challenges and implementing proactive solutions, the food industry can strive to build a more resilient and sustainable future.